There is no end to the quest of car perfectionism. To the car buyer who knows what he/she is buying, safeguarding a vehicle finish of pristine vision is mission number one against the onslaughts of the road. Automobile paint protection film (PPF) and ceramic coating have become the scorching topics in the surface-protection world. Over years the logical option was to merge them, and the big question that resonates both in write-ups of detailing shops and online discussion forums, is whether or not you should and can put ceramic coating over PPF. The answer is categorical yes. The physical strength of PPF blended with chemical strength and hydrophobic resistance of ceramic coating become a synergetic action and are much stronger than the sum of two products.
Nevertheless, the industry is not stagnated. The material science has been developed and the question about the necessity to combine these two technologies has become a thing of the past. The question that has to be considered more importantly now is how to combine them in order to achieve maximum performance, reliability and value. The guidelines provided below will examine the underlying principles of this protective pairing, describe the available application methods as well as introduce the high quality, factory direct technology that is redefining vehicle care.
PPF vs. Ceramic Coating: What’s The Difference?
The strength of their combination can be fully realized only after realizing the specific role played by every product. Although they can both safeguard the paint of your vehicle, they are entirely different in technology, and strengths. One can consider them a mechanical shield, and a chemical armour; one redirects motion energy, and the other rejects environmental pollutants.
Paint Protection Film (PPF) represents the transparent film of thermoplastic urethane (TPU) that is covered directly to vehicle painted surfaces. It has a secondary role to play as a thicker barrier; that comprises of a rigid, sacrificial layer that cossets the physical blow out of road debris. It will be the first line barrier against rock chips, grime, minor scratches, road tar and even abrasive materials. High grade PPF is normally 6 to 8 mils (0.006 to 0.008 inches) thick and usually includes self healing or auto healing whereby light scratches reverse themselves when heat is applied. Your car paint will not get spoilt as it would be under the protection of any physical damage.
A Ceramic Coating is a liquid polymer, which is applied by hand onto all the exterior surfaces of a vehicle. It contains either silica (SiO 2 ) or titanium dioxide (TiO 2 ) which, after curing creates an extremely thin, microscopic glass-like layer of protection and is very hard. It is not a physical shield as in the case of PPF but a chemical body armor. Its major advantages are outstanding chemical resistance to bird droppings, acidic contaminants, bug splatter, hard water markings, water markings, and chemical stain resistances aside from offering extreme gloss and extreme properties of hydrophobic surface which makes the vehicle extremely easy to clean.
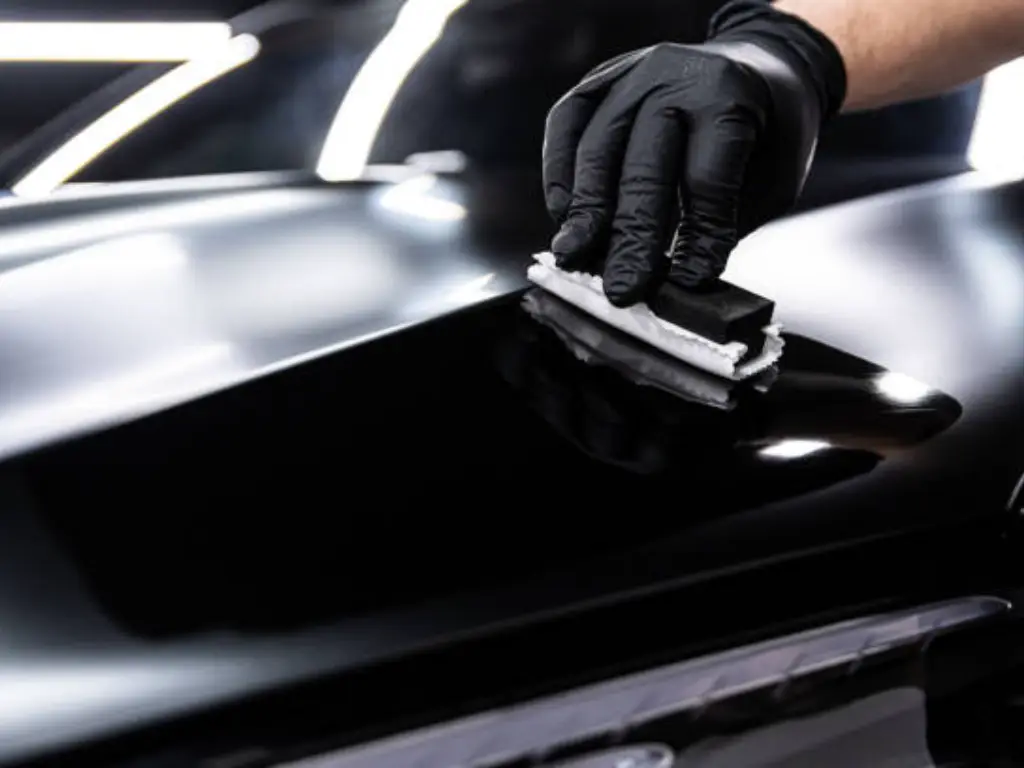
Here is a direct comparison of their core attributes:
PPF | Ceramic Coating |
Protects against physical damage like rock chips and minor scratches | Protects against chemical damage like bird droppings, tree sap, and road salts |
Resistant to abrasions | Repels grime and dirt, offering a smoother surface |
UV Protection to prevent yellowing | Hydrophobic properties to repel water |
Self-healing properties to eliminate swirl marks and light scratches | Chemical resistance to harmful contaminants |
Durability to extend the life of your vehicle’s finish | Gloss enhancement and deeper color vibrancy |
While each is effective on its own, it’s clear they protect against different threats. This is precisely why the concept of combining them became the gold standard for comprehensive protection.
Why Combine PPF with a Ceramic Coating?
The ensemble of the combination of PPF and a ceramic coating building a multi-layered defense mechanism comes out as an enhancement of the other leading to a traditional 1+1>2 effect. When evaluating the benefits one by one based on the product, although it is based on the products, it will turn out to be a win-win case.
For the PPF, the gains are transformative:
- Enhanced Gloss and Depth: although contemporary PPF is an incredibly clear product, it is not expected to improve the design. A ceramic coating on it forms an additional coating that will give the specific amount of gloss, depth and luster to them and the film is almost invisible making the paint work under it to have the look of candy with a layer of rich shell.
- Extreme Hydrophobicity: A naked PPF surface is not naturally hydrophobic. Water can sheet, instead of beading, and porches can adhere to the water. The film gives the ceramic coating its trademark water-beading effect which makes water and other contaminants slide off easily. This makes the washing up significantly easier and requires significantly less physical contact to keep your car clean, thus decreasing the likelihood of acquiring the scratches and swirl marks caused by the wash.
- Added UV & Chemical Resistance: Premium PPF has UV inhibitors in the film to prevent yellowing, but a ceramic coating is added as an extra sacrificial layer against ultra-violent uv rays. Above all it will offer an effective barrier against chemicals removed by bird droppings, tree sap, road salts etc that might otherwise have left marks or ruptured the best coat of the film as it persists with time.
- Extended PPF Lifespan: The ceramic coating provides a protective barrier that prevents any damage caused during a chemical and environmental attack, as it will act as the first line of offense, unlike the PPF whose integrity and aesthetics are kept intact. It accepts the punishment it receives day in day out so that the film does not wear out as quickly and also long life usability.
In the case of the Ceramic Coating, the advantages are primeval:
Ceramic coating is just like any other coating, and it must be applied on the surface. Using it on top of PPF makes it seem that the coating has the ideal canvas. The PPF offers a smooth, continuous, self-healing, and non-porous surface rather than a raw clear coat. The coating bonded to this ideal surface is the best surface and this surface produces the best performance. The PPF shields the coating on the bottom hence when a deep scratch can affect the film, it does not also cause an area of failure in the coating.
The Traditional Two-Step Application Process
To appreciate a technological leap of integrated solutions it is important to understand how this powerful duo is traditionally created. The traditional process is a multistic step that is labor intensive and takes a great deal of time, skill and expertise on the part of a way professional detailer.
Stage 1: Flawless PPF Installation & Initial Curing
It all starts with the job requiring the proficiency of Paint Protection Film. This in itself is an art because it also involves a surgically clean area and a lot of skill so that there is a seamless finish with no bubble. It is not possible to coat the film as soon as it has been installed. The slip solution in which the solution is installed must dry completely and the adhesive of the film must sink deep into the paint. This first stage of curing may not be completed until at least 24-72 hours, or even up to one week or more, depending on the installer, climatic conditions and paint application method. Hurrying this step is an avenue that can entrap moisture reducing quality of the film as well as the following coating.
Stage 2: Secondary Decontamination & Surface Preparation
Once the PPF is cured the vehicle is to be readied again to be given the ceramic coating. This is not just a wipe down. The removal of a clean layer of surface to which the coating should adhere is a sensitive yet an important process that takes place to produce the most sterile surface possible.
- Gentle Maintenance Wash: A pH-neutral soap and safe methods of washing the vehicle are used following the light dusting or dirt that has accumulated in the course of curing the car.
- Chemical Decontamination: Although the surface is newly created, it might have been afflicted with air containing iron particles. These gotta be dissolved typically with a pH-neutral iron remover so as not to damage the film.
- Final Panel Wipe: The whole PPF surface is carefully cleaned using a solvent that is of body shop grade panel prep or an Isopropyl Alcohol (IPA) solution. This gets rid then any remaining silicones, PPP installation remaining oils or residues that would inhibit proper molecular to form as a ceramic coating.
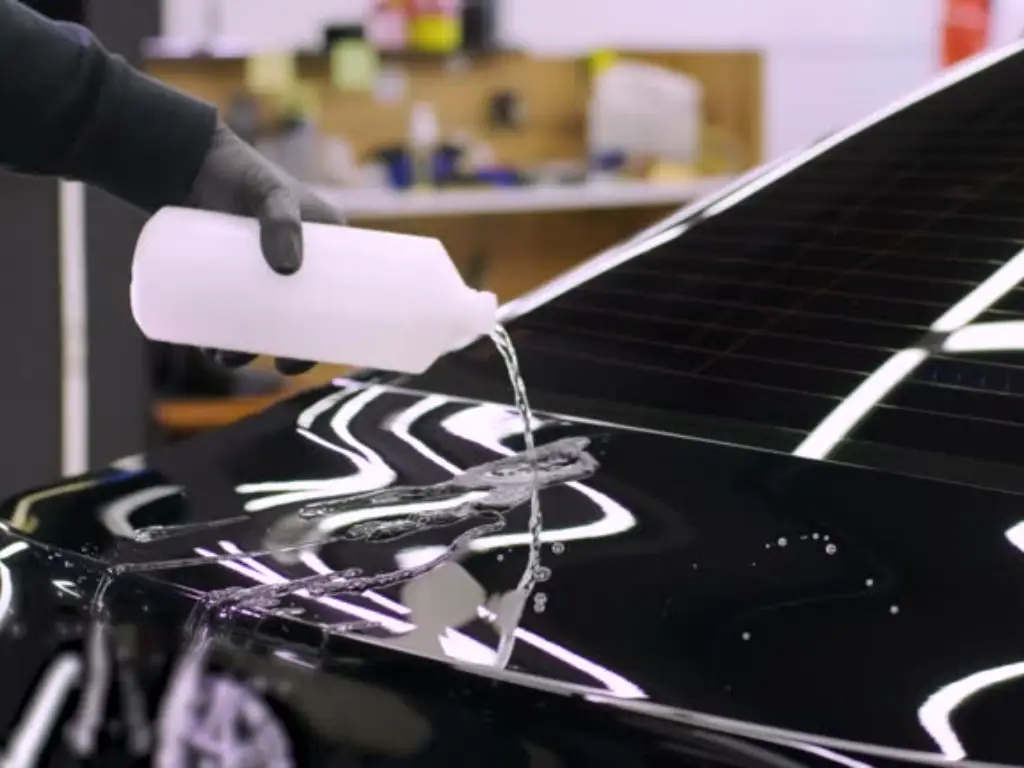
Stage 3: Meticulous Coating Application
Having the surface well prepared the technician is in a position to start the coating. This takes place inside an environment with temperature and humidity control. The liquid coating is deposited on the surface by applying very small manageable sizes (e.g. 2×2 ft squares) using a special microfiber applicator block that helps get even overlapped passes. The technician has to monitor the coating carefully as it flashes or start evaporating which is an indication that it is ready to be taken to the next procedure. The window ranges between 30 seconds and few minutes depending on the nature of coating and condition of the ambient.
Stage 4: Leveling and Final Curing
The coating should be applied in such a way that when it flashes, it requires to be leveled, i.e. smoothened gently by rubbing the coated region using a clean and high grade microfiber fair to remove the excess and obtain a flat coating that is free of streaks. Once the whole vehicle have been painted and smoothed a full and long curing period will commence. The car needs to stay absolutely dry and free of contaminants liable to exceed 24 hours, and the entire hardness and hydrophobic surface characteristics of the coating will take 1-2 weeks to establish.
When properly performed, this two-step procedure is powerful, yet complex, time-consuming and adds various variables that can interfere the final result.
A Smarter Way: The Rise of Integrated Coated PPF
The intricacies and possible variables of the conventional two step process have created the path to an enhanced and time effective process. The emerging industry is changing. Instead of a two-step-process, why not have a better solution which is factory-integrated?
Here, innovation makes a difference. The forward-looking manufacturers have created a new generation of Paint Protection Film that in turn has already a hydrophobic clear coat layer built-in. Since FlexiPPF is one of the main manufacturers and suppliers in the field of clear bra, they are one of the pioneers of this innovation. Our premium cine products have a unique ceramic top coat layer that is directly incorporated in the manufacturer process.
Advantages of Factory Pre-Coated PPF Technology
- Perfect Bonding & Durability: In the laboratory the ceramic film coating is molecular bonded to the thermoplastic urethane film under the most perfect boding conditions available. This produces a bound together interlaced structure that is significantly more strong and impervious to delamination, compared to the two-dimensional sticking on top of one another the hand application of a coating.
- Flawless, Even Finish: Manual work, even under the hands of a highly skilled technician is susceptible to variations such as irregular pressure, heat variation and humidity that may create swirl marks or uneven finishing. Factory integration by utilizing modern machinery incorporates the application of the coating to a microscopic level ensuring an optically clear, smooth and absolutely uniform finish.
- Saves Time and Installation Costs: This is one of the greatest advantages to the final customer. The two step procedure has two distinct labor costs involved and can render a vehicle inoperable for some days. Using a built-in product such as FlexiPPF, once the PPF installation is over, the protection is already done.
- Guaranteed Compatibility: Due to factory-integrated products, there is no chance of chemical incompatibility between a third-party ceramic product and a PPF particularly top coat or adhesive.
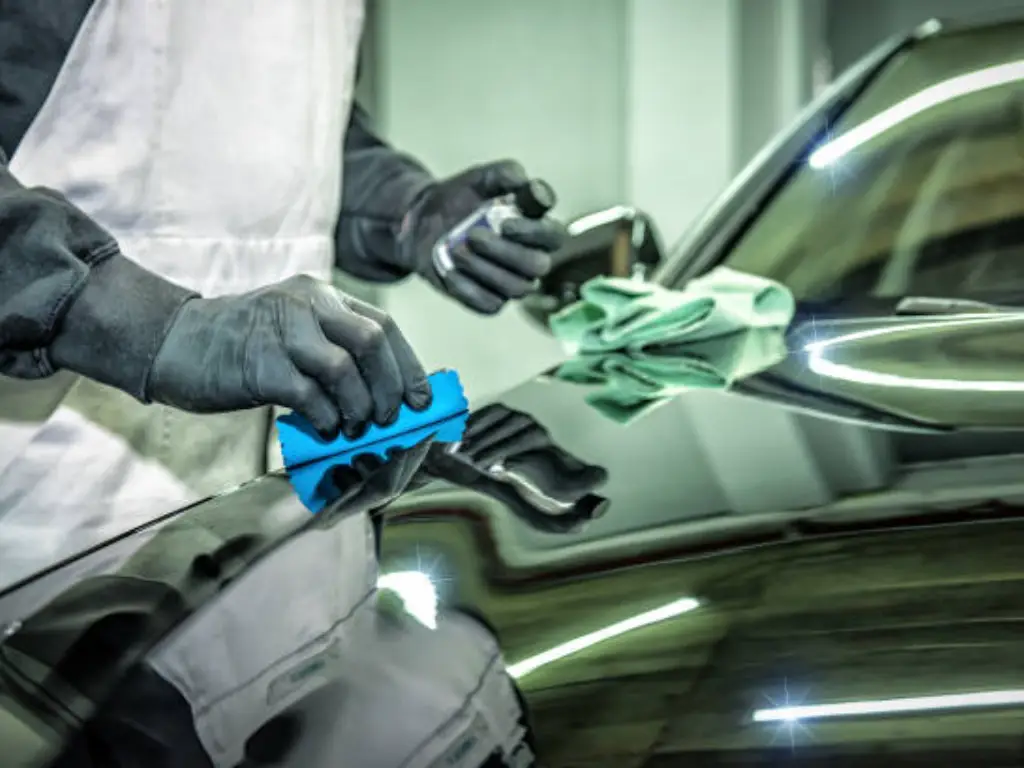
Does Coating Affect PPF’s Self-Healing?
This is a typical legitimate worry of informed consumers. The response is categorical: a quality and well-dosed ceramic coating will not prevent the self-healing capabilities of quality PPF, more so a factory-integrated one.
PPF has a self-healing layer of metals bonded together with elastomeric polymers. When there is a slight scratch or swirled line it is a dislocation in this polymer chain. These polymers are put into a relaxed and flowing state by the use of heat (by use of the sun, a heat gun, or warm water).
PPF coating is made in such a way that it is flexible. They will be tough but not too brittle so that they will crack, or hinder the motion of the underlying polymers. Since a part of the film should be an incorporated top coat produced by FlexiPPF, the flexibility is well adjusted to the urethane upper-coat. It is so programmed to be within the self-healing system, so that you will have the hardest chemical resistance and when you want, the scratches get healed.
Is This All-in-One Solution Right for You?
Vehicle protection is a matter of choice and it boils down to your objectives, your standards, and your criteria about the performance, and the peace of mind.
In case you are an intelligent car owner, who considers that car or truck is a major investment, the response is obvious. Ask yourself- Do you care about efficiency and technological advancement? Do you wish to protect your side mirrors, rocker panels and your total finish against severe elements and harsh chemicals? Would you like to maintain the quality of your car in the long run?
In a world where perfection takes priority, durability, long-lasting protection, and the smoothest finish on your vehicle is a given and the solution is clear and obvious, it is a fully invested ceramic-coated PPF through factory applied protection.
The Final Verdict: Your Best Protection Strategy
But is it possible to ceramic coat PPF? Indeed, and it has been over the years considered to be the best protection strategy. The discussion has changed, however. There is no longer a question on whether you should do this or not, but how you can optimally do this. Although the old technological approach of the two-step method is still an option it is now only a different generation of technology.
The next big thing in vehicle security is integrated cars. A single layer product which provides two types of protection, namely, physical and chemical is naturally better. It is also more hard wearing, is more uniform in its finish and more economical in its use. It is a smarter spend on the part of those customers who insist on the durability and quality. The next time you talk to a professional installer, do not just request PPF and a ceramic coating. Take the level of conversation up. Request an inclusive solution of them.